Batteries are widely used in daily life, such as automotive motorcycle batteries, agricultural sprayer batteries and so on. The battery is divided into water-soluble storage and dry batteries. Because the water solute is strongly acidic, it cannot leak out a little after sealing. Therefore, the size of the battery box casing is very high, and the mold is very high.
Experience in making battery box molds
With the development of society and economy and the improvement of people's living standards, plastic battery casings are widely used in various industries for its light weight, fast molding, low cost, good acid resistance and corrosion resistance The outer carrier also uses a plastic battery case. As one of the important components of the outer carrier, the quality of the battery case will directly or indirectly affect the quality of the battery.
Tools / raw materials
-
Injection mould
-
Pure PP new material
Method / step
First of all, we perform high-precision processing on the mold, and re-inspect it after processing. After the workpiece is taken off the machine, the quality control section of the knife will be used to make a comparison based on the shape.
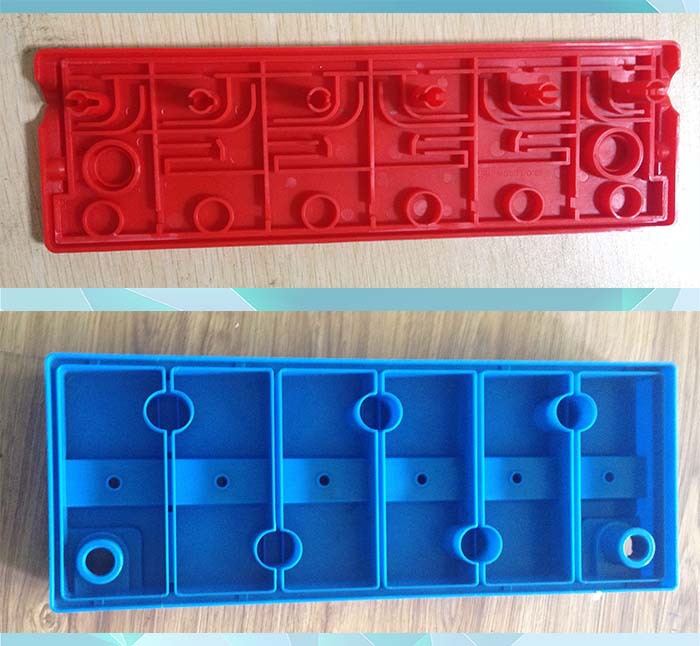
After the mold is assembled, pay attention to whether the gate size of the hot runner is consistent. If this is not the same, it will affect the size.
Control the injection pressure during injection to reach a normal value. Several samples were then stabilized. After the sample has cooled down naturally, cut all the products to be measured
Precautions
-
Main plastic stable size
-
Control processing size
Battery box mold design
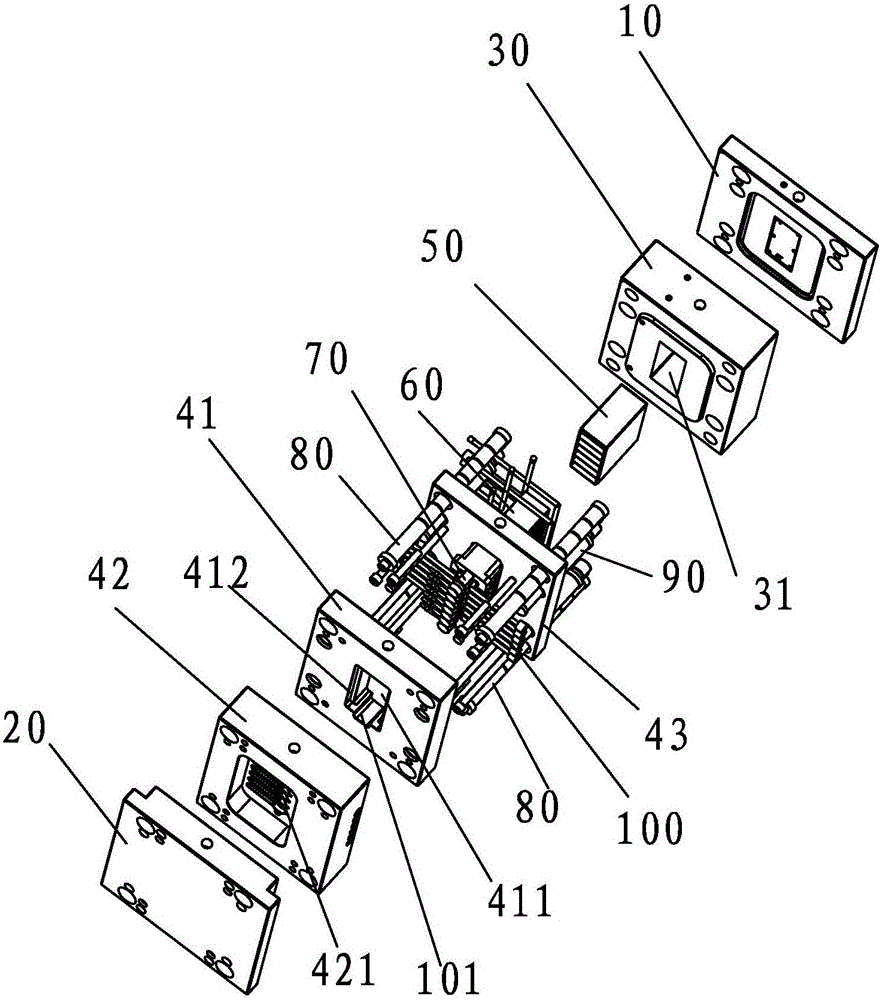
An battery box injection mold includes a face plate, a nozzle push plate, a nozzle plate, an A plate, a push plate, a fixing plate, a bottom plate, a first pulling plate, a guide post, a first fixing screw, a second pulling plate, a second fixing screw, Nozzle, nozzle edge, large tie rod, limit screw and fixed distance screw, wherein the panel is fixed on the fixed template of the injection molding machine and the base plate is fixed on the movable template of the injection molding machine.
The moving template moves together, the fixing plate and the bottom plate are fixed together by a first fixing screw, the nozzle plate and the A plate are fixed together by a second fixing screw, and a limit screw restricts the mold opening distance between the nozzle pushing plate and the panel, The first pull plate and the nozzle side limit the distance between the nozzle opening plate and the nozzle opening after the nozzle plate is opened, and the large draw rod limits the mold opening distance of the battery case, that is, the mold opening distance between the A plate and the pushing plate, and The push plate is pulled away to push out the battery case.
The second pull plate limits the distance from which the battery case is pushed out, that is, the distance between the fixed plate and the push plate. On the board, the sides of the guide post and the nozzle are opened on each template. Effect when the support serves as a guide die, wherein said first tie plate A spacer screws in the plate.
With the above-mentioned mold, after the injection molding, it is necessary to complete the demolding of the battery case through four mold openings, which has the disadvantages of a complicated mold structure and low production efficiency. At the same time, because it injects material from the top of the battery case, there will be a print at the disconnection of the material head from the bottom of the battery case after demolding, which affects the appearance and overall strength of the battery case.