The maintenance steps required for each injection molding location depend on the differential mold cycle. Here are some general guidelines that allow each mold user to use the useful operation of mold components such as hot runners, heaters, guide posts, and thimbles to prevent accidental environments.
-
1. Check for signs of rust or moisture at the diffuser – if you invent rust or wet signs around the hot runner vents, it means internal condensation or a broken water pipe. A wet sign can cause a fatal short circuit to the heater. If the dullness is not running all year round, but will be shut down at night or on weekends, the chances of this sign of cohesion will increase.
-
2. Remember to remind the operator not to “clear” the hot mouth at the gate – if the operator can see a small piece of stainless steel at the nozzle, it is probably a point assembly. "Clearing" this seemingly blocked tool often ruins the hot mouth. In order not to smash the hot mouth, please confirm the mouthpiece of the hot runner system before accepting the action, to ensure that all operators are well-trained and can recognize the mouth of all the different examples of their own.
-
3. Sliding Stops – Dealing with the dullness of running all year round, this should be done once a week.
-
4. Interactively verify the resistance of the heater – you should have measured the resistance at the beginning of the heater, and now it is time to measure again and compare. If the resistance value has a 10% up and down float, it is time to replace the heater to ensure that it does not go out of the way in the production process. If the initial resistance value has never been measured, it is measured once and the value obtained is used as reference data for later inspection of the heater.
-
5. Inspect the guide post and the guide bush for signs of wear – look for scratches or scratches, which are due to lack of lubrication. If the trace is just emerging, you can extend its life by adding more lubrication to the guide post and guide sleeve. If the wear and tear is already severe, it is time to exchange new parts. Otherwise, the cavity and core department may not be able to fit well, resulting in a thin wall of parts.
-
6. Check the water flow environment – connect a hose to the waterway exit and let the water pass through the water pipe to the bucket. If the water that is flowing out is not clear or has a color, there will be signs of rust, and if the water is not smooth, it means that it is blocked somewhere. If these problems are invented, all the water pipes will be drilled again, and the circulation will be carried out (or accept any of the most commonly used methods for liquidation). The water treatment system of the innovative workshop can guard against the problems caused by rust and clogging in the future.
-
7. Washing the thimble – After a year, the thimble becomes dirty due to gas accumulation and membranous impurities. It is recommended to wash it with mold rinsing every six to twelve months. After washing and cleaning, apply a layer of lubricant to the thimble to prevent scratches or breaks.
-
8. Inspect the radius of the hot nozzle for fractures – the fracture is caused by the clamping force from the plastic injection cylinder assembly when the loose, hardened plastic fragments remaining in the rigid nozzle are injected forward. The cause of the problem is probably that the central line is not aimed.
-
Consider the two possibilities when inventing the fracture. If the smashing is severe enough to prevent the appearance of a petal-like leak (a term used by mold users in the past: refers to plastic leakage between the guide sleeve and the rigid hot mouth), the sprue sleeve should be replaced.
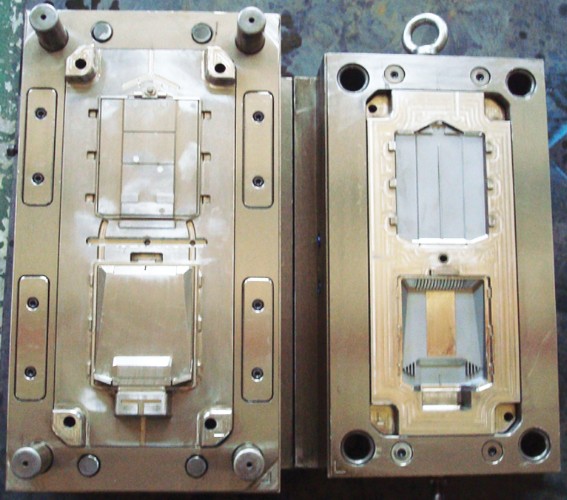