Good bottle mold design is a prerequisite for qualified mold manufacturing
Reasonable mold structure design is the premise of a qualified mold manufacturing. Our company's mold structure designer and product stylist have rich experience in design work, and can analyze all aspects of mold structure and product structure (including: mold removal Mold inclination, microcosm of product surface, design of pouring system, design of exhaust system, design of cooling system, etc.) The most important and easy problems of these molds will be tested repeatedly in the mold structure design to ensure that the product design is reasonable .
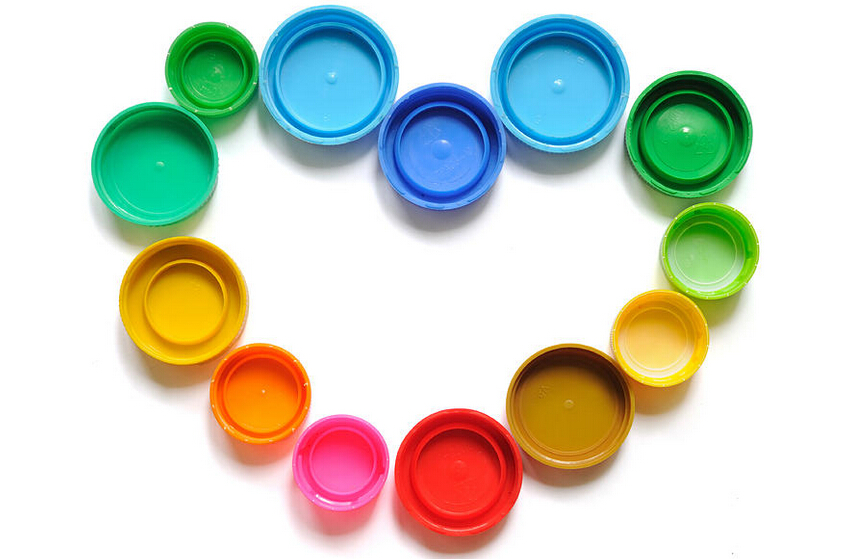
Hot runner bottle cap mold adopts PE (polyolefin) non-gate hot runner design commonly used in foreign countries, spring-type electric heating coil plus beryllium copper tube heating, the hot runner nozzle is controlled separately, and the mold is produced under automatic conditions without the need for frequent employees. Operation to reduce worker labor. The key parts of the mold (core, cavity, etc.) are made of excellent special steel for plastic molds and heat treated (HRC45) to ensure the service life of the mold and product quality. And the turning machining center is adopted to ensure the processing quality of parts and achieve mutual matching. The process is stable and the use effect is good, which is comparable to imported molds.
Taizhou Haichuan Molding Co., Ltd. specializes in developing and designing all kinds of bottle cap molds. According to the production needs of different manufacturers, there are ordinary and hot runner structures to choose from. Due to the use of an advanced cooling structure, gas-assisted demoulding. Eight molds have been produced as an example. The normal production cycle is within 22 seconds, and the production cycle of the hot runner mold is within 16 seconds.
Design of cap mould by seaco mould factory
The three times forced ejection technology, the balanced hot runner system and the universal mould base of the bottle cap mould adopted by BETOP bottle cap mould have strong innovation. The mould performance and quality have reached the domestic leading level and can be mass produced.
In general, the caps of beverage bottles such as mineral water and coke, or edible oil and other domestic liquids are threaded, and most of them are special threads. Its particularity is shown in the aspects of ending, subsection, subsection, short end and so on, sometimes even several characteristics are combined. Endcap and endcap is a professional common name, also known as screw thread endcap and endcap or mouse tail, which means a section of thread, under the condition of constant pitch, the beginning part changes from shallow to deep, gradually & quot; thick & quot;, the end part changes from deep to shallow, gradually & quot; thin & quot;. The common ending is usually completed in 1 / 3 to 1 week. The closeout completed within 1 / 3 week or even 1 / 10 week is called the closeout. The common thread has a feed groove and a return groove, so it often only sees the middle part of the thread, but not the head and tail. This kind of plastic bottle with special thread has a large consumption. One of the technical difficulties of this kind of mould processing is the processing of special thread. Many manufacturers have tried manual, electrical machining, milling (including CNC milling), casting and other processing methods, the results are not ideal.