Mould steel for bottle cap mould choose imported or domestic
Domestic mold materials can not fully meet the needs of mold manufacturing industry. Many molds with high performance, long life and urgent delivery date still have to use imported mold materials. The price of imported materials is very high, 3-5 times higher than that of domestic materials. To this end, chairman Lin said that in fact, in addition to a few varieties, some research and development are needed, most products and size specifications in China are capable of development, and the key problem lies in how to ensure the quality stability of domestic die steel and shorten the delivery time of steel. He believes that at present, cooperation between mould material enterprises and mould manufacturing enterprises should be strengthened. Because the development and development of mold market is a systematic project, the departments of mold material development, production, sales, promotion, mold design, manufacturing and mold use, etc. are required to organize, cooperate vigorously, feed back the problems and requirements of mold manufacturing and use in time, develop and trial production, technical consultation, pre-sale and after-sale services, and vigorously Promote the application of high-performance mold materials with stable quality, make our mold materials catch up with the world's advanced level rapidly, and promote the rapid development of our mold industry.
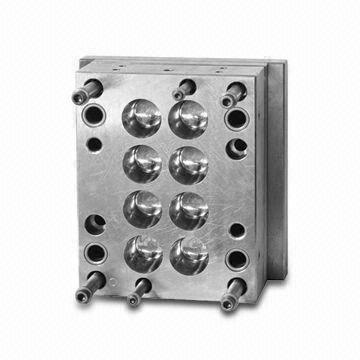
Material requirements of plastic products for bottle caps
The working conditions of the plastic mould are different from that of the cold stamping die. Generally, it must be operated at 150 ° C-200 ° C. besides certain pressure, it must also bear the influence of temperature. According to the different use conditions and processing methods of plastic mold, the basic performance requirements of plastic mold steel are summarized as follows:
-
1. Sufficient surface hardness and wear resistance
The hardness of plastic mould is usually below 50-60hrc, and the mould after heat treatment shall have enough surface hardness to ensure that the mould has enough rigidity. Due to the large pressure stress and friction in the filling and flow of plastic, the mold is required to maintain the shape accuracy and dimensional accuracy stability, so as to ensure the mold has sufficient service life. The wear resistance of the die depends on the chemical composition of the steel and the hardness of the heat treatment, so improving the hardness of the die is conducive to improving its wear resistance.
-
2. Excellent machinability
In addition to EMD processing, most of the plastic forming molds also need some cutting and fitter repair. In order to prolong the service life of cutting tools, improve the cutting performance and reduce the surface roughness, the hardness of steel used in plastic mould must be improved.
-
3. Good polishing performance
High quality plastic products require a small surface roughness of the cavity. For example, the surface roughness of injection mold cavity is required to be less than the level of ra0.1-0.25, and the optical surface is required to be RA & lt; 0.01nm. The cavity must be polished to reduce the surface roughness. The steel selected for this purpose requires less impurities, fine and uniform structure, no fiber directionality, and no pitting or orange peel like defects during polishing
-
4. Good thermal stability
The parts of plastic injection mold are often complex in shape and difficult to be processed after quenching. Therefore, the ones with good thermal stability should be selected as far as possible. When the mold is processed by heat treatment, due to small linear expansion coefficient, small heat treatment deformation, small size change rate caused by temperature difference, stable metallographic structure and mold size, it can be reduced or no longer processed, which can ensure the precision of mold size Degree and surface roughness requirements.
Carbon steel of 45 and 50 grades has certain strength and wear resistance, and is mostly used for mold base materials after tempering treatment. High carbon tool steel and low alloy tool steel have high strength and wear resistance after overheating treatment, which are mostly used for forming parts. However, high carbon tool steel is only suitable for manufacturing small size and simple shaped parts due to its large heat treatment deformation.
With the development of plastic industry, the requirements of the complexity and precision of plastic products are higher and higher, and the requirements of mold materials are also higher. For the manufacture of complex, precise and corrosion-resistant plastic molds, pre hardening steel (such as PMS), corrosion-resistant steel (such as PCR) and low-carbon maraging steel (such as 18ni-250) can be used, all of which have good cutting, heat treatment and polishing properties and high strength.
Special steel for production of bottle cap mould
Professional design of the bottle cap mold, unique hot runner process and perfect cold runner design structure, plus a good cooling water circulation system, so that the mold can be produced in a high-speed environment, and the products produced are the same inside and outside. The mold steel adopts the special steel suitable for each mold production, so that the hardness after heat treatment can reach more than 50 degrees.
Scope of business: we can provide one bottle cap mould with 1 to 72 cavities for: mineral water bottle cap, mould five gallon mould hot runner system oil bottle cap, mould soy sauce lid mould other bottle caps, mould daily cosmetics lid mould, specialized in making high quality bottle cap mould and bottle blank, uniform design of flow channel, efficient and reasonable cooling system, short injection cycle, long mould life, affordable price and fast delivery We are looking forward to friendly cooperation with your company to create a win-win situation.
The mould factory is committed to the research and manufacture of bottle cap mould. After years of hard work, it has accumulated rich design technology and manufacturing experience, especially mastering certain core technology for the manufacture of mineral water bottle cap, oil cap and pharmaceutical bottle cap mould.