Injection medical equipment mold company is a tool maker for producing plastic medical products; it is also a tool maker that gives medical plastic products a complete structure and precise dimensions. Injection molding is a processing method used in the mass production of certain complex shapes. Specifically, the heat-melted plastic is injected into a mold cavity by an injection molding machine at high pressure, and after cooling and solidification, a molded product is obtained. So what are the characteristics when processing injection molds for medical equipment? Let's talk about how the medical company making the mould in process.
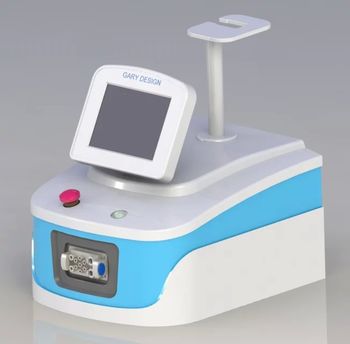
-
1. Long process flow, tight processing time. For injection molded parts, many are complete products that are matched with other parts, and in many cases, they have already been completed in other parts. Kong Yin looks forward to the completion of the injection molded parts. Because of the high requirements on the shape or dimensional accuracy of the product, and because of the different characteristics of the resin material, after the processing of the medical equipment mold is completed, it is necessary to frequently test and correct the mold, which makes the development and delivery very serious.
-
2. Professional division of labor, dynamic combination. Medical equipment molds are produced in small batches and generally belong to the production of a single piece. However, medical equipment molds require a large number of scale parts. The mold base is as small as a thimble. These cannot and cannot be completed by a single manufacturer, and the processing technology is complex The use of popular equipment and numerical control equipment is extremely unbalanced.
-
3. Off-site design and processing. Medical equipment mold processing is not the ultimate goal, but the user proposes a perfect product design. Medical equipment mold processing manufacturers design and process medical equipment mold products according to user requirements. This has caused the situation of product design, medical equipment mold design and processing and product production to be carried out in different places.
-
4. The cavity and core have a three-dimensional profile. The external and internal shapes of the plastic parts are directly formed by the cavity and the core. The processing of these complex three-dimensional profiles is more difficult. The blind-hole inner molding of the cavity is generally processed. If the traditional processing method is used, not only Workers are required to have a high level of craftsmanship, many auxiliary fixtures, many tools, and long processing cycles.
-
5. High precision and profile quality requirements, long service life requirements. At present, the dimensional accuracy of general plastic parts is IT6-7, the roughness of the profile Ra0.2-0.1μm, and the dimensional accuracy of the responsive injection medical equipment mold parts must reach IT5-6, and the roughness of the profile Ra0.1μm or less. The roughness of the laser disc recording surface must reach 0.02-0.01 μm, which is the level of mirror processing. This requires the profile roughness of medical equipment molds to be less than 0.01 μm. Long-life injection medical equipment molds are very necessary to advance high efficiency and reduce costs. At present, the life of injection medical equipment molds generally requires more than one million times. Careful injection molds should use a rigid mold base, increase the thickness of the template, add support columns or conical positioning elements to prevent deformation of the medical equipment mold under pressure, and sometimes the internal pressure can reach 100 MPa. Ejection assembly is the main factor that affects the deformation and dimensional accuracy of the product. Therefore, the appropriate ejection point should be selected so that the mold is ejected everywhere. The structure of high-precision injection medical equipment molds adopts the mosaic or full-spliced structure, which requires the machining accuracy and exchangeability of medical equipment mold parts to be advanced.