there are few reasons for dissatisfaction with the filling of plastic products in the office. As a senior mold manufacturer, of course, it will know how to solve it. Now let me explain to you, what are the reasons for the dissatisfaction with the filling of plastic products?
There are mainly the following reasons for the dissatisfaction with the filling of the product: 1. The temperature of the barrel and the nozzle is too low; 2. The mold temperature is too low; 3. The amount of material is not enough; The gate is too small; 7, the injection time is too short; 8, the holding time is short; 9, the nozzle clogged with impurities or the spring needle valve nozzle fails; 10. the quality or area of the part exceeds the maximum injection volume or maximum injection area ; 11, there is no proper vent hole in the cavity. All of the above are reasons, but the main reasons are lack of material and improper injection pressure and speed (including the excessive pressure loss caused by resistance).
Solution:
1. Machine side: ① Due to the instability of the machine's plasticizing amount or heating power, a machine with a large amount of plasticizing and heating power should be selected; ② the wear of the screw and the barrel or the rubber head or The damage will cause the material to return and the actual filling modulus will not be correct; ③ The failure of heating systems such as thermocouples or heating coils will cause the actual temperature of the barrel to be too low, which will also bring some dissatisfaction to the filling of plastic products; ④ injection cylinders The wear of the sealing elements caused oil leakage or backflow, which could not reach the required injection pressure; ⑤ The inner hole of the nozzle is too small or the nozzle center is not adjusted properly, which causes excessive resistance and consumes pressure.
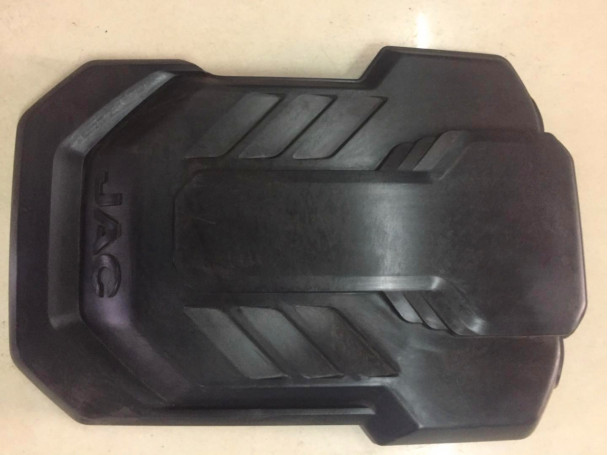
2. For the mold: ① The temperature of the mold is too low, which makes feeding difficult, and the mold temperature should be appropriately raised. Of course, if there is a mold temperature machine, these problems can be solved well. ② The mold cavity Unbalanced distribution. The wall thickness of the part is too thin, resulting in excessive pressure consumption and insufficient filling. The wall thickness of the whole part or part should be increased or an auxiliary flow or gate can be set up to solve the problem of insufficient filling. ③ If the flow path of the mold is too small, pressure loss will occur; if it is too large, the glue will be weak; if it is too rough, it will cause dissatisfaction of the part. The size of the runner should be appropriately set, and the transition between the main runner and the runner, the gate, or the corner of the runner should apply a proper arc transition. ④ Poor exhaust of mold. The material that enters the cavity is blocked by the pressure of the gas that is too late to be exhausted, causing filling dissatisfaction. You can make full use of the gap exhaust of the screw or reduce the clamping force and use the parting surface to exhaust. If necessary, an exhaust channel or air hole must be opened.
3. Reasons for the recurrence of the dissatisfaction of the product: ① When the particle size of the plastic raw materials is uneven, the amount of the added material may be uncertain. ② The wear of the screw head, rubber ring and rubber washer of the screw is too large, which may cause dissatisfaction due to the sliding of the melt and the backflow between the screw and the barrel. ③ The cooling system of the inlet fails, which makes the unloading quantity unstable. ④ Insufficient injection volume setting of the barrel, that is, the cushion cushion is too small, which will cause the injection of the product for a long time and there will be dissatisfaction with the product.