The amount of plastic used in automobiles has become an important indicator of the level of automobile design and manufacturing. At present, more than 10% of domestic automobile materials are made of plastic, from exterior parts such as bumpers, skirts and fenders to dashboards. Interior parts such as door panels and uprights, as well as engine peripherals such as front frames, covers and intake manifolds, plastics are everywhere. Most automotive plastic parts are injection molded, with short molding cycles, high production efficiency, and low manufacturing costs. However, injection molding may have many defects. The defects of automobile injection molded parts and their solutions are collected .
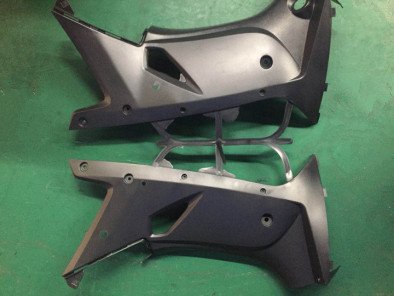
First, tiger skin pattern.Tiger skin pattern often appears on large-sized automotive injection parts such as bumpers, dashboards, door panels, and pillars. It is a surface defect of wavy stripes. The stripes are approximately perpendicular to the direction of melt flow and form on the surface of the injection molded part The engraving with different luster looks like the pattern on tiger skin, commonly known as tiger skin pattern.
Tiger skin is easy to produce on injection-molded parts with thin walls and large processes. It has the following characteristics:
(1) Periodically changing light and dark stripes appear on the surface of the injection molded part;
(2) The stripes are approximately perpendicular to the flow direction of the melt;
(3) The stripes are divided into bright and dark areas, the gloss of the bright area is high, and the gloss of the dark area is poor;
(4) If the appearance of the injection molded part is light, the back is dark, and the two appear alternately.
Reasons for automotive injection parts :
1. The more toughening materials in the material, the easier the tiger skin pattern phenomenon appears. The toughened material is stretched and sheared during the injection molding process, causing slight deformation, which causes the melt to flow in an unstable manner, which results in tiger skin. Materials with poor toughness rarely show the appearance of tiger skin, such as reinforcing materials, non-toughened nylon, polybutylene terephthalate and other materials. Tiger skin rarely occurs during the molding process. Polypropylene (PP), which is used in automotive injection molded parts, is highly prone to tiger skin defects due to the addition of toughening components such as elastomers due to the high impact resistance required.
2. The thinner the wall thickness of the injection molded part, or the farther the filling flow distance, the larger the flow length ratio, the more likely the melt will be unstable to flow during the filling process, and the easier it will be to produce tiger skin. Properly increasing the wall thickness of the injection molded part, or shortening the filling distance of a single gate, can reduce the mold filling resistance of the melt, ensure the stability of the melt flow, and help eliminate tiger skin marks. However, today, with the increasing demand for lightweight vehicles, thinning is the development trend of automotive injection molded parts, so it is not realistic to eliminate tiger skin by increasing wall thickness.
Automotive injection parts solution:
In terms of mold design, increasing the runner diameter and enlarging the thickness and width of the gate are effective measures to eliminate tiger skin. The gate thickness should preferably be 0.7-0.8 times the wall thickness. The purpose of this move is to reduce the pressure loss of the melt in the runner and the gate, and reduce the expansion effect of the mold when entering the cavity.
In the design of the mold, the straight gate, side gate and fan gate with gradual transition should be used as far as possible to avoid the use of latent gates and spot gates with gradually decreasing cross-sectional areas. Practice has proved that latent gates, spot gates, or small side gates are easy to produce tiger skin.
In terms of injection molding process, melt temperature, mold temperature and injection speed are several important parameters affecting tiger skin texture. Generally speaking, increasing the melt temperature and mold temperature and adjusting the injection speed are beneficial to eliminate tiger skin marks. The use of lower injection speed is beneficial to eliminate tiger skin lines, because the melt flow is more stable at low speed.