Modern electricians are everywhere. News about electrical appliances processing, bicycle die-casting parts, mobile phone middle plate die-casting, radiator processing, mechanical parts processing, mechanical parts die-casting, electronic parts die-casting, aluminum alloy die-casting parts processing.
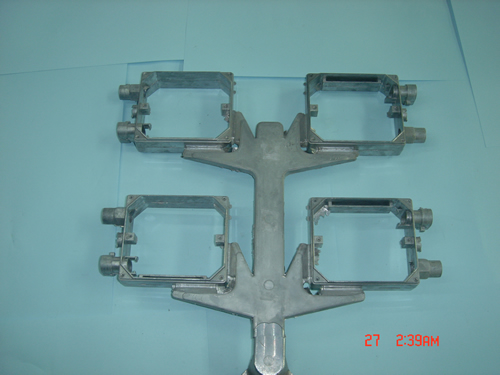
Die-casting molds are a large class of molds. With the rapid development of China's automobile and motorcycle industries, the die casting industry has ushered in a new period of development. At the same time, higher requirements are also placed on the mechanical properties and life of the die. In order to meet the increase in performance requirements, it is still difficult to meet the new mold materials. Various surface treatment technologies must be applied to casting molds. Die-casting molds achieve surface treatments with high efficiency, high precision and long life. Pressure casting is a process of high pressure and high speed full mold and die-casting molten metal repeated contact with hot metal, so the die-casting mold has high heat resistance, thermal fatigue wear, corrosion resistance, impact toughness, red hardness, Good release properties. Therefore, the technical requirements for the surface treatment of die-casting molds In recent years, new technologies for the surface treatment of various die-casting molds have continuously emerged, but they can generally be divided into the following three categories:
(1) Improvement of traditional heat treatment process;
(2) Surface modification technologies, including surface treatment, surface thermal diffusion strengthening, and electric spark strengthening technology;
(3) coating technologies, including chemical plating.
Improvement of traditional heat treatment process
The traditional heat treatment process for die casting molds is quenching and tempering. Since various materials can be used as die-casting molds, the same surface treatment process and process can have different effects in different materials. SKOV recently proposed the pretreatment technology of the base material for the mold base material and surface treatment technology, and the treatment technology, and proposed different mold materials based on the traditional process to improve the performance of the mold and increase the life of the mold. Another development direction of heat treatment technology is to combine the traditional heat treatment technology with advanced surface treatment technology to improve the service life of the die. If the carbonitriding chemical treatment method is combined with the conventional quenching and tempering process (ie carbonitriding and carbonitriding quenching) NQN composite strengthening, it not only has a high surface hardness and an increase in the depth of the effective hardened layer, and the layer hardness gradient The distribution, stability and fire and corrosion resistance are improved in order to obtain good performance at the same time, and the performance and surface quality are greatly improved.
Development status of aluminum processing in China
From the macro level of economic growth, the meso perspective of industry evolution, and the micro behavior of enterprise development, we all find that the current aluminum industry's transition from primary electrolytic aluminum smelting to deep processing will become an inevitable trend. Aluminum processing products are generally priced in the form of "aluminum price + processing fees". When the total downstream demand and structural increase are rapidly increasing, companies with technological advantages, channel advantages, cost advantages, and location advantages not only have processing fees It can be guaranteed, and there is also the possibility of improvement. If the factors of capacity expansion are added together, the growth of performance will be rapid and significant.
In recent years, China's aluminum profile industry has grown rapidly and has completely developed into a highly competitive industry. As of the end of 2010, there were 824 aluminum profiles enterprises above the designated size in China. After the rapid development stage and the fierce market competition, the basic pattern was initially formed. At present, there are many manufacturers in the aluminum foil industry in China, and the industry concentration is low. No one company has a significant market share, and no one company can have a decisive influence on the development of the entire industry. In 2010, the national aluminum foil output was about 2 million tons, and there were more than 250 companies engaged in aluminum foil production, with an average output of about 80,000 tons. The average scale is small, there are many small enterprises, and there is excessive competition in the field of low value-added products .
With the rapid growth of China's aluminum profile industry, the sales revenue of the aluminum profile industry will also increase year by year. Statistics show that from 2005 to 2010, the compound annual growth rate of sales revenue of China's aluminum profile industry was 35.20%. According to the current domestic and international economic situation, combined with 2005-2010 sales data of China's aluminum profile industry and China's economic growth data, a rough estimate of the compound annual growth rate of sales revenue of China's aluminum profile industry from 2011 to 2015 is 20%. In 2015, China Aluminum The sales revenue of the profile industry will reach 10498 billion yuan. With the rapid development of the aluminum foil downstream industry, its demand for aluminum foil will continue to increase. By 2012, aluminum foil consumption will reach 1.8 million tons, 2013 will reach 2.1 million tons, and the compound annual growth rate from 2011 to 2013 will reach 17 %.