The design knowledge base of the aluminum alloy low-pressure casting department adopts a modular idea. According to the function of the system, three sub-modules of the Dongguan die-casting knowledge base are designed, an explicit knowledge module, a three-dimensional module, and a rule knowledge module.
The design knowledge base of the aluminum alloy low-pressure casting department adopts a modular idea. According to the function of the system, three sub-modules of the Dongguan die-casting knowledge base are designed, an explicit knowledge module, a three-dimensional module, and a rule knowledge module.
The ultimate goal is the low-pressure casting process KBE system aluminum alloy to obtain more detailed cards, so the database will require the design of a stored procedure that involves explicit knowledge, so the establishment of explicit knowledge modules, in order to facilitate management and invocation, combined with knowledge acquisition Mechanism, explicit knowledge is divided into different attributes storage.
The design process is usually a process related to geometry (such as the size of the casting system of the casting system). The KBE-based design scheme can be reflected in the design of the three-dimensional solid model, which will undoubtedly make the design more intuitive. Based on this idea, a three-dimensional solid model. In this module, the STL file of the aluminum alloy low pressure casting system needs to be die cast in Dongguan. To facilitate STL files, each STL file in the database is described qualitatively and quantitatively.
In the design process, general principle knowledge (tacit knowledge) is often used as a guide, so it is a process based on many rules, such as the pressure of determining some basic formulas of the inference module based on inference, and the real-time dynamic knowledge of database knowledge calls the corresponding rules. To make the rule knowledge module provided by the knowledge base.
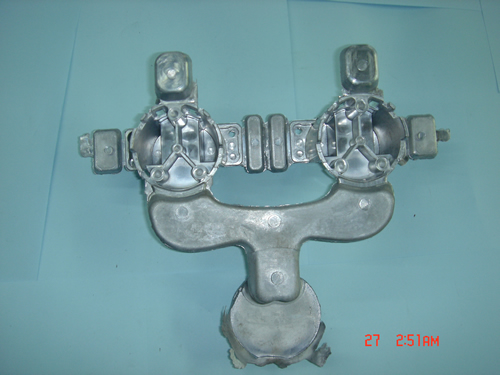
The density of cast aluminum alloy is lower than that of cast iron and cast steel, but the specific strength is higher. Therefore, aluminum alloy castings can be used under the same load conditions to reduce the weight of the structure. Therefore, aluminum alloy castings have been widely used in the aviation industry, power machinery and transportation machinery manufacturing. Aluminum alloy has good surface gloss, good corrosion resistance in the atmosphere and fresh water, and has been widely used in civil ship manufacturing. Pure aluminum has good corrosion resistance in acidic oxidizing media such as nitric acid and acetic acid. Pure aluminum and aluminum alloys have good thermal conductivity, and are used in heat exchange equipment in chemical production. They have good thermal properties and requirements for mechanical parts, such as internal combustion engine cylinders and pistons.
Aluminum alloy has good casting properties. Due to its low melting point (pure aluminum 660.230c, the melting temperature of aluminum alloys is generally around 730 ~ 750oc), it can be widely used in metal casting and pressure casting methods to improve the inherent quality, dimensional accuracy, surface finish and production of castings effectiveness. Due to the large latent heat of solidification, under the same weight conditions, the solidification time of aluminum alloy is much longer than that of cast steel and cast iron.
Casting aluminum alloy castings has many advantages, making it one of the most popular casting products for the development of the casting industry and customers. With the development of aluminum alloy casting technology in the future, it will be displayed on a larger stage.