Plastic molds chinese manufacturer tell you how to get high quality plastic mold. In the process of obtaining important products, this information focuses on the structure and model of thermoplastic molds.
Chinese Plastic molds have the characteristics of high production efficiency, low labor intensity, long service life, etc., and can form complex plastic products. The structure of a plastic machine is determined by factors such as the form and complexity of the plastic machine. this product. Although plastic molds have various structural forms, they can be divided into two parts: dynamic mode and fixed mode.
The mold is fixed, the mold is closed to form a cavity and the pouring system, the mold is fixed, the mold is separated from the mold, the product is fixed on the fixed template of the plastic machine, and the nozzle mouth or the pouring sheath is directly connected.
The movable mold is mounted on the movable mold of the plastic machine and moves with the template to separate or approach the separated portion. The general core and ejector mechanisms are in this section. Plastic molds usually consist of the following parts.
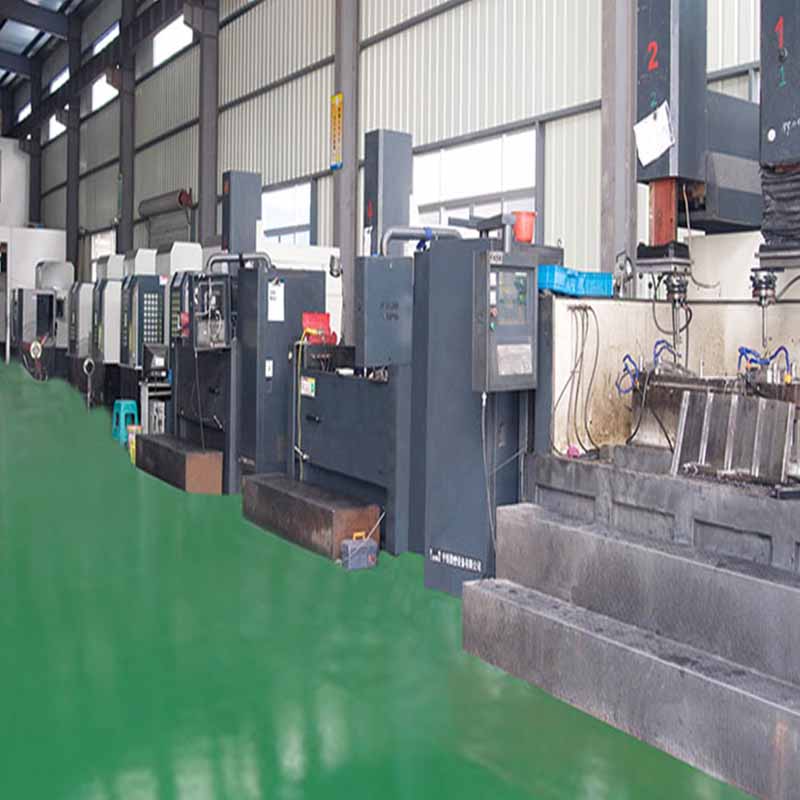
Cavity
The mold cavity is part of a mold that directly forms a plastic product. It usually consists of a punch (the inside of the molded product, the external shape of the molded product, the core or molding rod, inserts, etc.) the module and the fixed mold related parts. In order to ensure the surface of the plastic product is smooth and easy to demold, Where the surface is in contact, the roughness should generally be small, preferably less than Ra0.2.
Gating system
The gating system refers to the partial flow of the plastic melt that is injected from the nozzle into the mold cavity, and is divided from the main flow, and the flow is formed by the gate and the cold forming point.
2.1 Main channels:
The main flow channel is the part of the mold that connects the injection nozzle to the cavity of the manifold or channel. The main channel is concave at the top of the spherical surface so as to contact the nozzle. The inlet diameter is slightly larger than the nozzle diameter, usually 4 ~ 8mm, and gradually increases along the feeding direction. The magnification angle is generally 3 ° ~ 5 °, easy Flow out of the mold.
2.2 Diversion:
The splitter is a channel connecting the main channel and the door in a multi-cavity. In order to fill the cavity with equal speed, the splitter should be symmetrical and equidistant in the mold.
The shape and size of the cross section of the diversion channel have an influence on the flow of the melt, the release of the product and the ease of mold manufacture. Common shunts are trapezoidal or semi-circular in cross-section, and are opened on the mold and demolded. In order to meet the injection process and manufacturing requirements, under the premise of the flow path, the cross-sectional area and length should be reduced as much as possible, and the symmetrical isometric distribution should be reduced.
The shape and size of the cross section of the diversion channel have an influence on the flow of the melt, the release of the product and the ease of mold manufacture. The common mode shunt is trapezoidal or semi-circular in cross section, and the mold is opened on the mold. Under the premise of meeting the injection process and manufacturing requirements, the cross-sectional area and length of the runner should be minimized to reduce the transfer channel
Gate 2.3:
The door is connected to the slide (or main channel) and the channel's cavity. Public doors are: direct door, side door, panel door, ring door, spoke door, fan door, point door, submersible door, ear door, etc. The function of the gate is to control the flow so that the frit of the flow channel is filled with the mold cavity and does not return to facilitate the separation of the product from the flow path. The area should be small, not large, and small but not easy. The position of the door is generally selected where the product is thickest and does not affect the appearance.
2.4 Cold material point:
The cold material hole is a hole located at the end of the mainstream road to capture the nozzle between the two sprays to prevent the gate or the gate from being blocked, and to prevent the cold material from entering the cavity and generating internal stress. The frequency of cold material holes is generally 8 ~ 10mm, and the depth is 6mm. In order to facilitate the hair out of the mainstream road, cold bottom material is usually used for the support of the peeling rod of the curved hook or sinker.
Boot section
The mold part and the movable part are respectively installed on a fixed template and a movable mold plate of the plastic machine, and are in a state of reciprocating closing and opening in the plastic process. In order to ensure that the movable mold and the mold clamp the mold guide parts, there are usually guide posts, guide holes or dynamic molds in the mold to match the inner and outer tapered surfaces. Some devices from the injection mold are provided with guide members to prevent the top plate from moving horizontally in order to avoid distortion during the process of spraying the top plate.
Classification of core traction mechanism
Items with outside or side holes must be laterally shaped before being ejected, and side punches or side cores must be removed before disassembly.
5. Eject the device
Also called peeling device. The product is cooled and shaped in the mold. In order to remove the product, the mold is generally set outside the equipment. The product is ejected from the mold; some are ejected from the mold, depending on the type of ejector and the type of ejector set on the mold.
Cooling and heating system (water flow)
In order to meet the requirements of the mold temperature injection molding process, the mold is provided with a cooling or heating system. Cooling systems usually provide cooling water channels in the mold, heating the interior of the mold or mounting around heating components, such as electric heating rods, electric panels
Exhaust system (airflow)
In order to exhaust the original air in the cavity during the injection process, the exhaust groove is usually opened on the parting surface, but the small product is not exhausted and can be directly used for exhausting part of the surface. The core and mold with gaps can exhaust Function, so there is no need to open another exhaust port.
8.Mould mounting parts
The mold mounting component has two functions. One is to reliably install the mold on the plastic machine template; the other is to use the mounting component to adjust the thickness of the mold so that the thickness of the mold meets the requirements of the plastic machine.