Of course, the silicone injection molding process is mature.
At present, many pacifiers on the market are made of silicone injection molding. Our factory has such machines, which are specially targeted at the medical supplies industry. Silicone injection molding is similar to injection molding, but the machine is not the same as the equipment, and the feeding system is different. It uses a two-component translucent liquid silicone rubber material, which is an A glue and a B glue. This process is more environmentally friendly and the material is more stable. It is safer for human use than the vulcanization process.
Silicone is a special silicone injection molding machine.
It is cold-injected, and the mold is heated!Liquid Silicone Rubber is divided into A rubber and B rubber, and the ratio of the two is controlled by a quantitative device to 1: 1, and then fully mixed through the Static Mixer, injected into the injection tube, and then Production of injection molding. Inject liquid silicone into the hot runner mold to make silicone products, which can achieve the advantages of one-time molding, no waste, and automation.
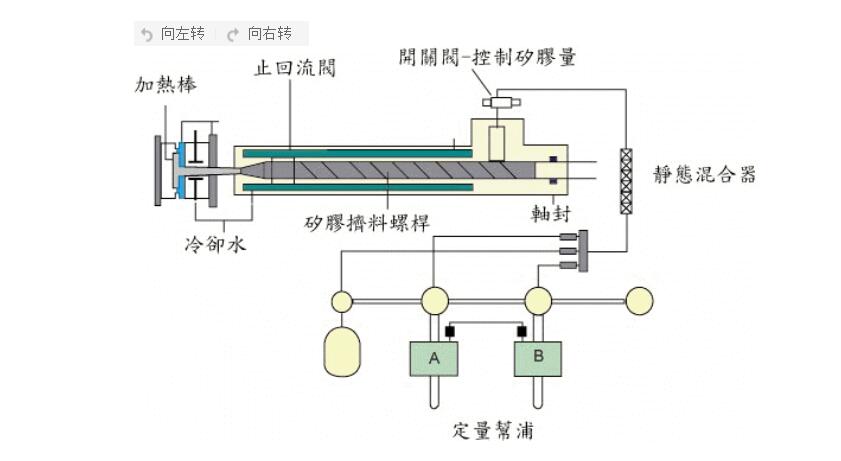
Silicone mold and plastic mold have three differences:
First, the composition of the two is different:
-
1. Silicone mold composition: Generally consists of five components: base rubber, cross-linking agent, catalyst, filler and additives. Usually base rubber, cross-linking agent and filler are made into one component, and the catalyst is a separate component. Therefore, the mold silica gel is also called two-component vulcanized silica gel and RTV-2 room temperature curing silica gel.
-
2. The composition of plastic molds: the structures of blow molds, casting molds and thermoforming molds are relatively simple; the structures of compression molds, injection molds and transfer molds are more complex, and there are more parts that make up such molds.
Two, the classification is different:
1. Classification of silicone mold:
-
(1) Solid silica gel is mainly used for compression molding products. Such as silicone sleeves, silicone tableware, silicone molds, silicone buttons, etc., liquid silicone is mainly used for extrusion molding products, such as silicone nipples, silicone tubes, etc.
-
(2) Excellent high temperature resistance of heat-insulating silicone pads. Silicone (food-grade silicone) can withstand high temperatures of 200 ° C and can be used for a long time. The raw materials for this product meet food-grade standards and pass FDA food-grade testing. It is tasteless and non-toxic. Manufacturers According to the production, the color and shape can be customized.
2. Classification of plastic molds:
According to different molding methods, plastic processing mold types corresponding to different process requirements can be divided, mainly including injection molding molds, extrusion molding molds, blister molding molds, high foaming polystyrene molding molds, and the like.
Third, the two have different uses:
-
the use of silicone mold: mainly used in the toy gift industry, craft gift industry, furniture decoration industry, character reproduction, architectural decoration industry, resin craft industry, unsaturated resin craft industry, candle craft, plastic toy industry, gift stationery Industry, plaster craft gift industry, mold manufacturing industry, Poly industrial products, simulation of animal and plant sculpture, Buddha carving crafts and other industries, product replication and mold making.
-
The use of plastic molds: China's plastic molds have been driven by high-tech drive and pillar industry application needs to form a huge industrial chain, from the upstream raw and auxiliary materials industry and processing and testing equipment to downstream machinery, automobiles, Motorcycles, home appliances, electronic communications, construction materials and other major application industries, plastic mold development is alive.