Car lights are also composed of a base and a lamp housing. The material of the base is generally a thermosetting material --- BMC, and the lamp housing can be processed from PMMA, PP, ABS and other materials. It is generally two-color or three-color or even four-color. In the actual injection molding production, different molecular compound plastic melts have very different flow properties, the structure of the
lamp mold is also very different, and the mold environment and process conditions are also different. It is difficult to control the quality of the product . Because of this, during the production process, it is necessary to repeatedly adjust the process parameters to optimize the product yield and quality.
The relationship between lamp type and material
Correspondence between the lights of different parts, color, material, number of processing cycles, number of cavities and molding time.
Note: The BMC (DMC) material is a subtraction of Bulk (Dough) molding compounds, that is, the ball-shaped mold molecular compound plastic. It is often referred to in China as not reaching the maximum limit of polyester agglomerate molecular compound plastics. The main raw materials are GF (chopped glass fiber), UP (not reaching the maximum limit gum), MD (filler calcium carbonate) and various additives in a dough-like prepreg.
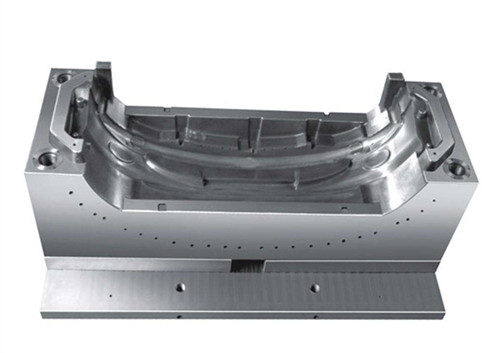
In the production process of two-color car lights, it should be particularly noted that the injection distance of the two-color injection molding machine, the center distance between the two screws should correspond to the center distance of the two-color production model.