With the advent of the era of electric vehicles and driverless technology and new energy vehicles, lightweight design of automobiles will be an inevitable trend in automotive design, and plastics will inevitably make the lightweight design of automobiles a reality. The extensive use of plastics in the automotive industry will definitely bring a new historical opportunity to the plastics industry and the automotive injection mold industry.
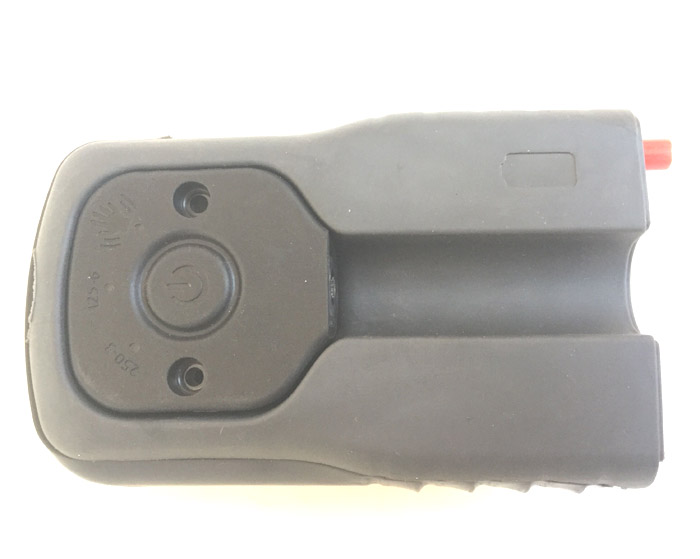
The proportion of automotive injection molds on the interior and exterior trims Behind the rapid development of the automotive industry is the development of the automotive mold industry. Especially in recent years, the development of the world's automotive mold industry is changing with each passing day, and automobile demand for molds is also increasing. In a new car, about 500 pairs of automotive injection molds are needed. In developed countries of the automotive industry, the market share of automotive products has exceeded 60%, and this trend continues to rise. It can be said that the proportion of injection molds in automobile molds is very large, and the importance is self-evident.
Lightweight, parts, lightweight, materials
, advanced technology of automotive interior and exterior plastic injection molds
Automotive injection molds are not fundamentally different from other injection molds, but also have many characteristics of their own. Because the added value of automotive injection molds is generally high, many advanced technologies (such as sequence valve hot runner control technology, internal parting surface technology, low-pressure injection technology, etc.) are preferentially developed and applied in automotive injection molds.
1. Sequential valve hot runner control technology (SVG technology)
Sequential valve hot runner control technology (SVG technology) is a new class of controlled hot runner technology. The glue is fed in sequence through the cylinder control, which solves the traditional multi-point synchronous glue The appearance of the product is difficult. It can effectively avoid defects such as welding marks and air pockets on the interior and exterior trims of automobiles, reduce flow length, reduce molding pressure, and play a huge role in interior and exterior trims with strict appearance requirements.
2. Low-pressure double-layer injection mold technology
The so-called low-pressure double-layer injection mold, also referred to as low-pressure injection mold, is a new type of injection mold technology. It traditionally relies on manual coating and vacuum suction of female and male parts, and it is directly injected into the mold. The main principle of low-pressure injection molds is: plastic with lower injection pressure flows on the cloth. When opening the mold, first hang the cloth on the hanging pin of the front mold, then close the mold, inject, and then take the part. The products produced by this technology have a special soft cloth on the surface, which greatly improves the decoration, feel and aesthetics. Therefore, the low-pressure injection mold technology is widely used in middle-to-high-end automobiles, and is generally used in parts such as automobile map pockets and automobile ABC pillars.
The main principle of the low-pressure injection mold is that the injection pressure is low and flows on the cloth. When the mold is opened, the cloth must be hung on the hanging pin of the front mold, and the mold is closed, injected, and then taken.
3. Automotive bumper internal parting injection mold technology
In automotive injection molds, for automotive bumper products, the mold is usually designed with advanced internal parting surface technology. The advantage is that the parting clip line is hidden on the non-appearance surface of the bumper, and the appearance clip line cannot be seen after assembly on the car, which will not affect the appearance of the product. However, this technology is more difficult and structurally complicated than the outer parted bumper, and the technical risk is higher. The mold cost and mold price will also be much higher than the outer parted bumper. Is widely used.